Lean & Environment Toolkit: Chapter 1
Introduction: Getting Started with Lean & Environment
Purpose of This Toolkit


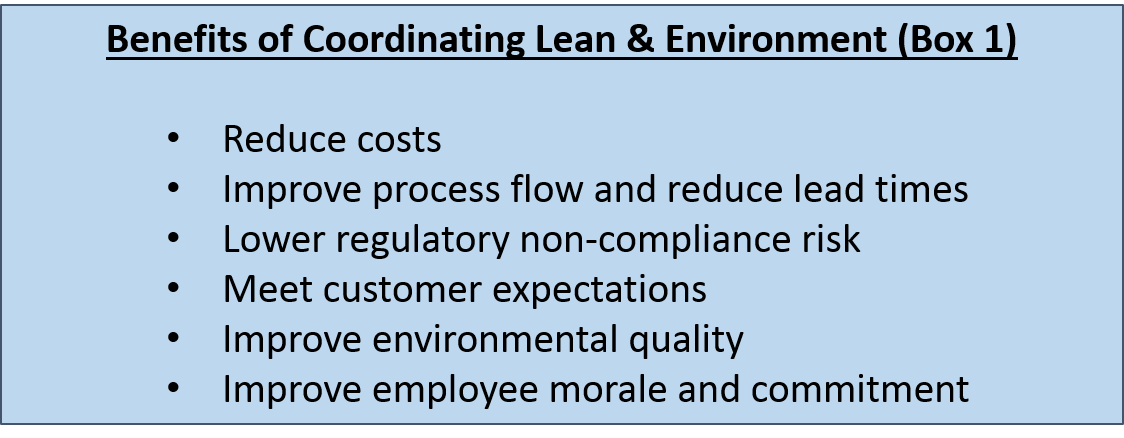
Key Questions Addressed by the Toolkit
Lean works well when it focuses on identifying and eliminating non-value added activity. Environmental improvement efforts that have potential to distract Lean efforts from this prime focus will likely not get much traction. By contrast, this toolkit contains strategies and techniques that can seamlessly enable Lean practitioners to easily identify environmental wastes and improvement opportunities alongside the myriad other wastes and improvement opportunities uncovered by Lean. To accomplish this, the toolkit aims to answer the following questions:

Why should I identify environmental waste in my processes? Environmental wastes do not add value to the customer. Environmental wastes can also directly affect production flow, time, quality, and cost—making them ripe targets for Lean initiatives. In many cases, the costs associated with pollution and wasted energy, water, and raw materials can be significant. This chapter (Chapter 1) discusses the business case for eliminating environmental waste.
How will I know when I see environmental waste? Some environmental wastes are easy to see. Containers of solid and hazardous waste are visual indications of environmental waste. Health and environmental risks posed by certain chemicals or materials can be more difficult to see, although they can represent costly non-value added aspects of a process or product. Chapter 2 provides examples of environmental wastes and describes organizational strategies that will make it easier to know when you see them.
Where should I look for environmental wastes? Environmental wastes can be found in almost any process. Processes requiring environmental permits—such as painting, metal finishing, and hazardous waste management processes—are often a good place to look for environmental improvement opportunities. If your organization has an environmental management system (EMS), your EHS personnel may have already identified key environmental impacts associated with each of the organization’s processes. Chapter 3 discusses how value stream mapping (VSM) tools and techniques can be used to help Lean practitioners see environmental wastes in processes. Chapter 4 discusses how to identify and address environmental wastes during kaizen rapid improvement events.
How do I measure the environmental impacts of a process? Measurement of key environmental wastes associated with a process can pinpoint those wastes that are most important to track over time. For example, chemical use and hazardous waste generation may be important to measure for one process, while water use may be most important to measure for another process. Chapter 3 discusses techniques for integrating environmental metrics into value stream maps. Appendix B includes information on environmental metrics that are often used by companies and facilities.
Where can I find environmentally preferable alternatives to my current process? EHS professionals in your organization may have ideas and information regarding environmentally preferable processes, equipment, and materials. In addition, numerous organizations, including EPA, have developed technical assistance resources and programs to assist organizations to improve the environmental and operational performance of processes. Chapter 4 discusses several useful resources and technical assistance networks. There are also Pollution Prevention Resources in Appendix D.
Why Use This Toolkit

Below are three key reasons why business leaders, Lean practitioners, and environmental, health, and safety (EHS) managers have pursued efforts to coordinate Lean and environmental management activities.
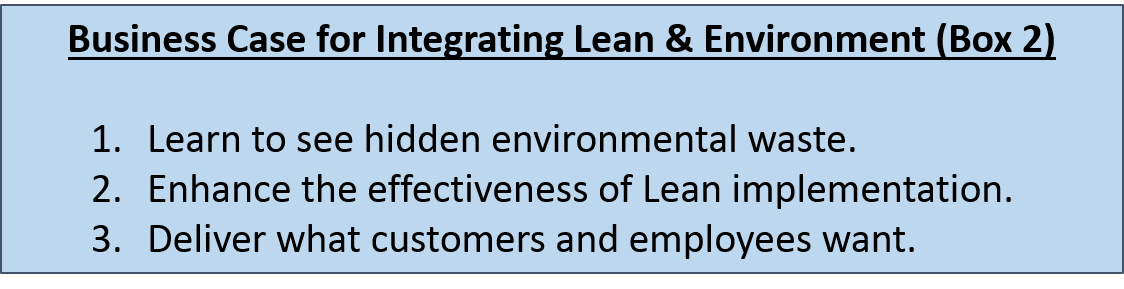
1. Learn to See Hidden Environmental Waste and Hazards
Learning to see and eliminate waste is a cornerstone of Lean initiatives. There is one type of waste, however, that often goes unaddressed (or under addressed) by Lean initiatives—environmental waste. When grouped together, environmental wastes can result in huge costs to business. These costs include raw material and disposal costs, as well as costs for compliance management activities and pollution control equipment.
Lean’s focus on eliminating non-value added activity is excellent at driving down the volume of material, water, energy, chemical usage, and wastes, producing important competitiveness and environmental benefits. The environmental risk and full lifecycle impacts that materials and chemicals pose to human health and the environment, however, are rarely considered during Lean implementation. Learning to see environmental wastes during Lean efforts can open significant business improvement opportunities, further strengthen Lean results, and improve environmental performance.

Chemical substitution, process changes, and other strategies can reduce the need for such non-value added activities. For these reasons, learning to see and eliminate environmental wastes can greatly improve the time, quality, and cost results of Lean initiatives.
2. Enhance the Effectiveness of Lean Implementation
Explicit coordination of Lean and environmental initiatives can lead to compelling organizational and environmental improvement results. For example, Lean thinking can be applied to various environmental management processes, such as chemical and waste management. Companies have found that as much as 40 percent of their chemical supplies were going unused and directly becoming hazardous waste as they expired on the shelf or became obsolete. Using Lean principles to improve chemical and waste management processes can have big pay-offs for environmental performance and bottom-line results.
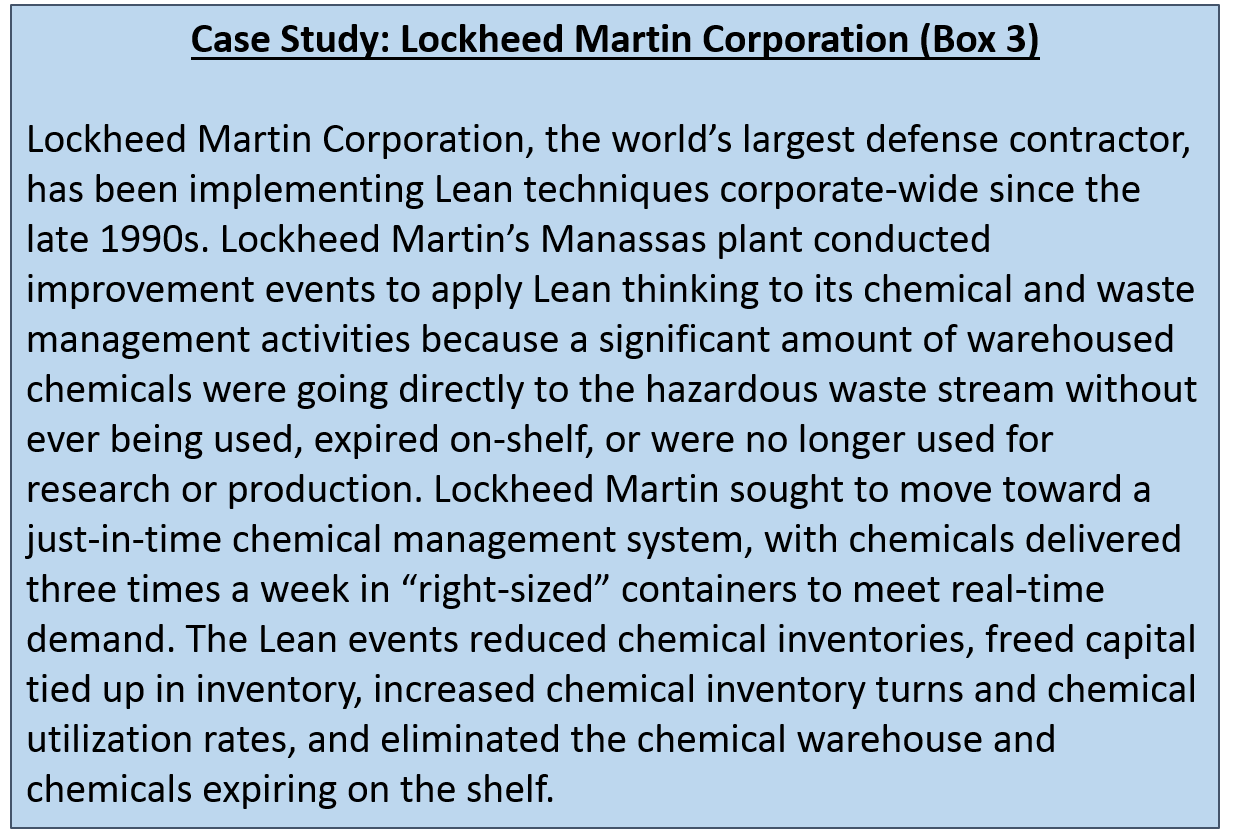

Making changes to monument processes can require approval or permits from environmental regulatory agencies, as well as special work practices or control measures, all of which can be difficult to accomplish within rapid timeframes. EHS personnel can help to identify environmentally friendly process alternatives, and ensure that process changes can be made as quickly as possible.
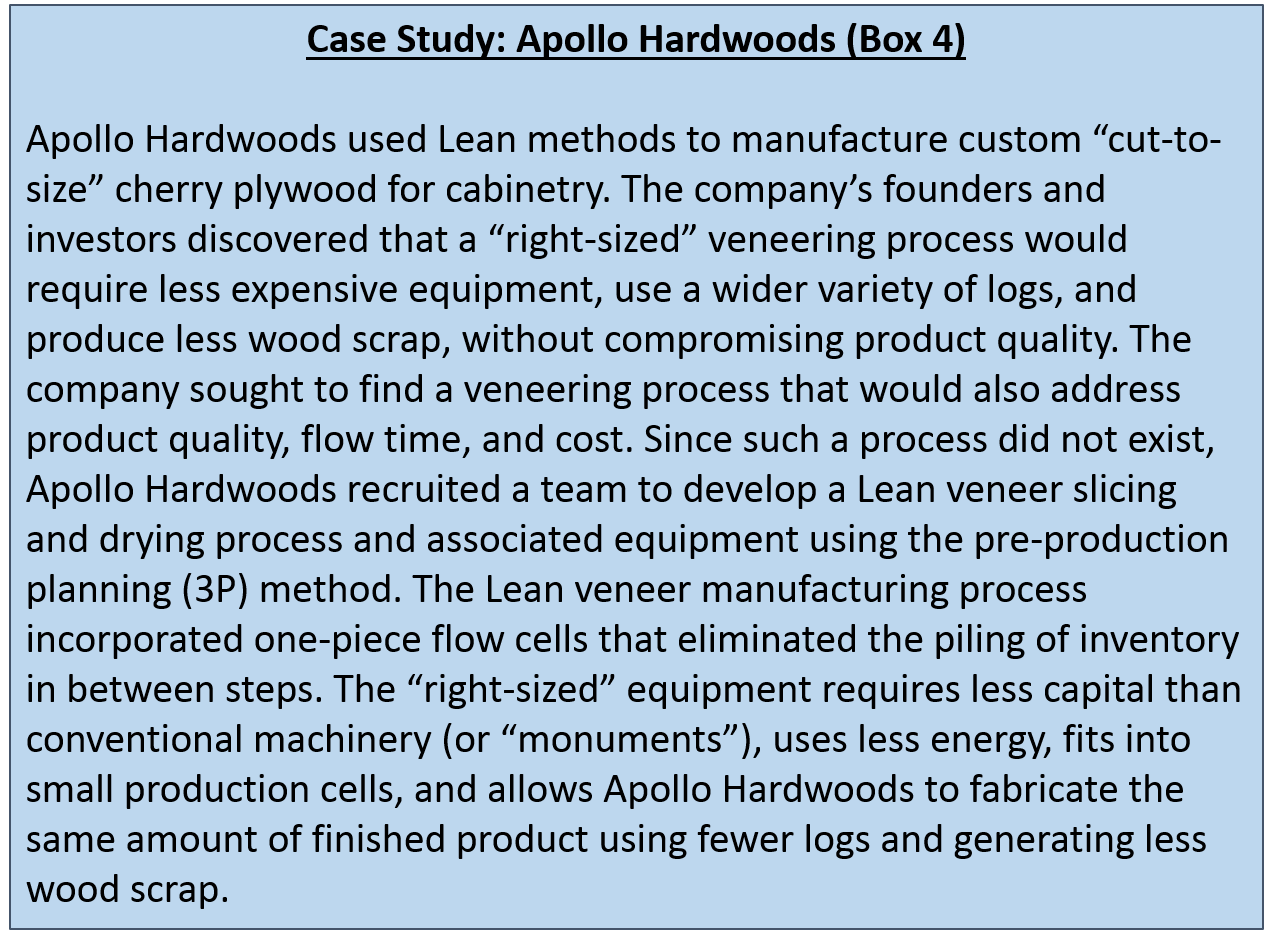
3. Deliver What Customers and Employees Want


Explicit consideration of environmental waste in Lean initiatives can also improve the work environment for employees. Similar to ergonomic concerns, eliminating environmental hazards can reduce potential worker exposure to toxic substances and create a clean, safe workplace.
In addition, employees want to do the right thing. When employees take pride in their work because they believe it has broader benefits to their community and the world, there can be a substantial positive effect on organizational morale. This can empower employees and further enhance productivity.
Conclusion
Summary
This toolkit provides practical strategies, tools, and techniques for incorporating environmental considerations into already existing Lean initiatives in an effort to improve Lean results and add value to your organization.
There are three key reasons why business leaders, Lean practitioners, and EHS managers pursue efforts to coordinate Lean and environmental management activities.
- Learning to see and eliminate hidden environmental wastes during Lean implementation can lead to more efficient production by improving the time, quality, and cost results of Lean initiatives. Chemical substitution, process changes, and other strategies can reduce the need for non-value added activities—such as regulatory compliance management and investment in pollution control equipment—that might otherwise be overlooked by Lean alone.
- Coordination of Lean and environmental management can facilitate more process improvement and make it easier to apply Lean to processes with environmental regulatory constraints. EHS personnel can assist Lean implementation by anticipating and addressing environmental constraints such as the need to obtain permits, and by identifying environmentally friendly process alternatives.
- A significant competitive advantage can be attained by providing customers with products and services with less environmental impacts, and by improving the work environment for employees.
Your Thoughts
Now that you have finished this chapter, reflect on what you read by answering these questions:
- What did you learn in this chapter that was particularly useful?
- Do you need any more information to fully understand the business case for identifying and eliminating environmental waste? How strong is the business case for doing this in your organization?
- What ideas do you have for helping your organization learn to see environmental wastes?
Toolkit Navigation
- Contents & Acknowledgements
- Preface
- Chapter 1: Introduction: Getting Started with Lean & Environment
- Chapter 2: Identifying Environmental Waste
- Chapter 3: Value Stream Mapping
- Chapter 4: Kaizen Events
- Chapter 5: 6S (5S + Safety)
- Chapter 6: Conclusion and Implementation Strategies
- Appendix A: Lean Methods
- Appendix B: Basic Environmental Measures for Lean Enterprises
- Appendix C: Lean Event EHS Checklist
- Appendix D: Pollution Prevention Resources
- Appendix E: 6S Safety Audit Checklist