Lean & Chemicals Toolkit: Chapter 4
Chemical Management in the Lean Organization
- Lean Strategies and Chemical Use
- Lean Approaches to Chemical and Hazardous Waste Management
- To Consider
- Footnotes
- Toolkit Navigation
Lean Strategies and Chemical Use
Classic Lean manufacturing strategies typically involve the conversion from batch-and-queue production with large material inventories to right-sized manufacturing cells with one-piece flow and just-in-time material delivery. This fundamental reconfiguration of production activities has major consequences—and improvement opportunities—for chemical use and management.
In this context, four Lean strategies can be used to dramatically reduce chemical use, waste, and risk while supporting core Lean goals. These include cellular manufacturing and right-sized equipment, just-in-time delivery, right-sized containers and kitting, and point-of-use storage.
Cellular Manufacturing and Right-Sized Equipment



Second, right-sized equipment typically requires only a fraction of the chemical inputs of conventional equipment. Conventional manufacturing equipment is often over-sized to accommodate the maximum anticipated demand. Since purchasing a new large piece of equipment is often costly and time-consuming, engineers often design in additional buffer capacity to be sure that the equipment does not bottleneck production. Conventional, oversized equipment can lead a company to use significantly more chemicals than needed to get the job done. For example, a facility with one large, 1000-gallon part cleaning and degreasing tank may only wash a few small parts in each batch. A shift to much smaller, 10-gallon, right-sized parts cleaning tanks may be all that is needed to get the actual work done, saving hundreds of gallons of chemicals.
Just-in-Time Delivery



- Lower likelihood of a large chemical spill or accident
- Reduced need to purchase and maintain chemical storage tanks
- Reduced space needed for storing chemical inventories
- Reduced need for chemical spill prevention equipment and measures
- Elimination of certain regulatory, permitting, and reporting requirements, including the need to develop and implement Risk Management Plans required by Section 112(r) of the Clean Air Act (see example in Box 12)
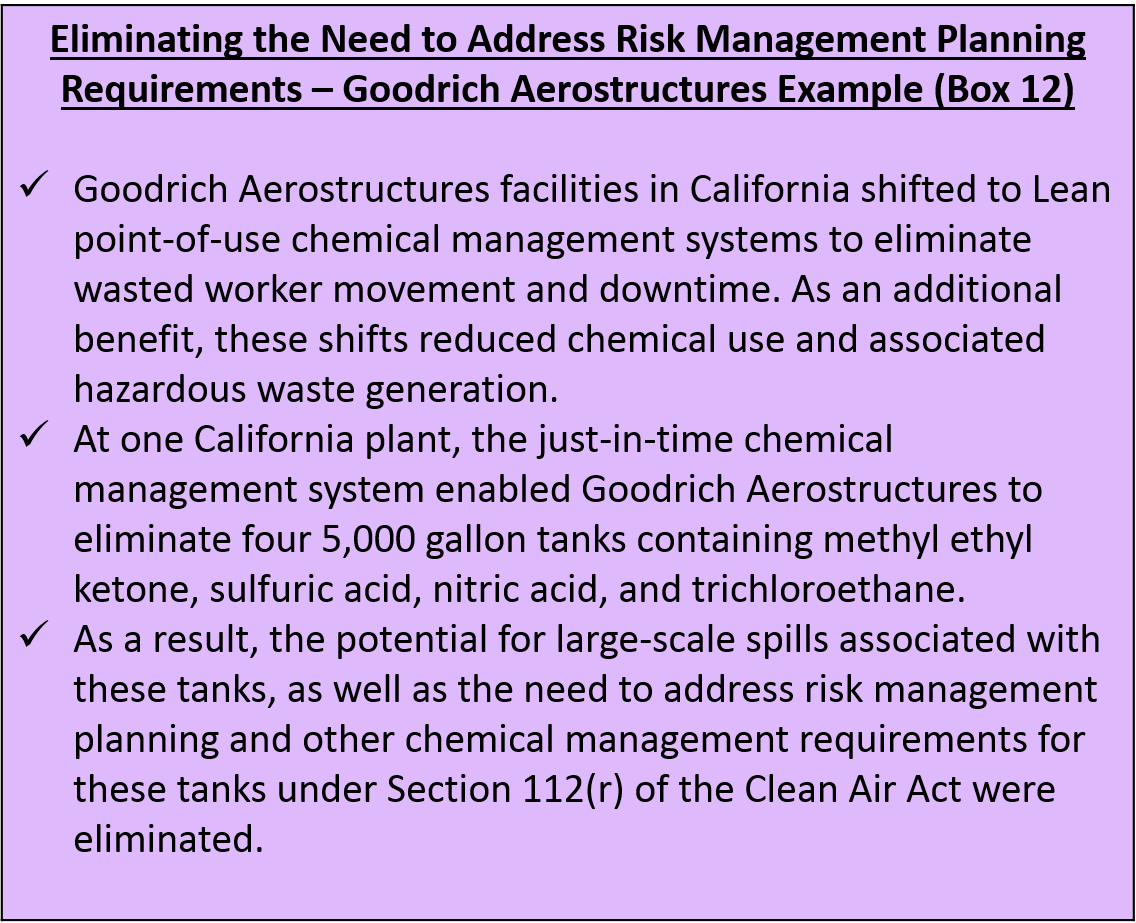
While moving to JIT chemical deliveries can increase the per-unit cost of chemical purchases, many organizations find that the total system cost advantages are significant, driven by the benefits discussed above.
Right-Sized Containers and Kitting

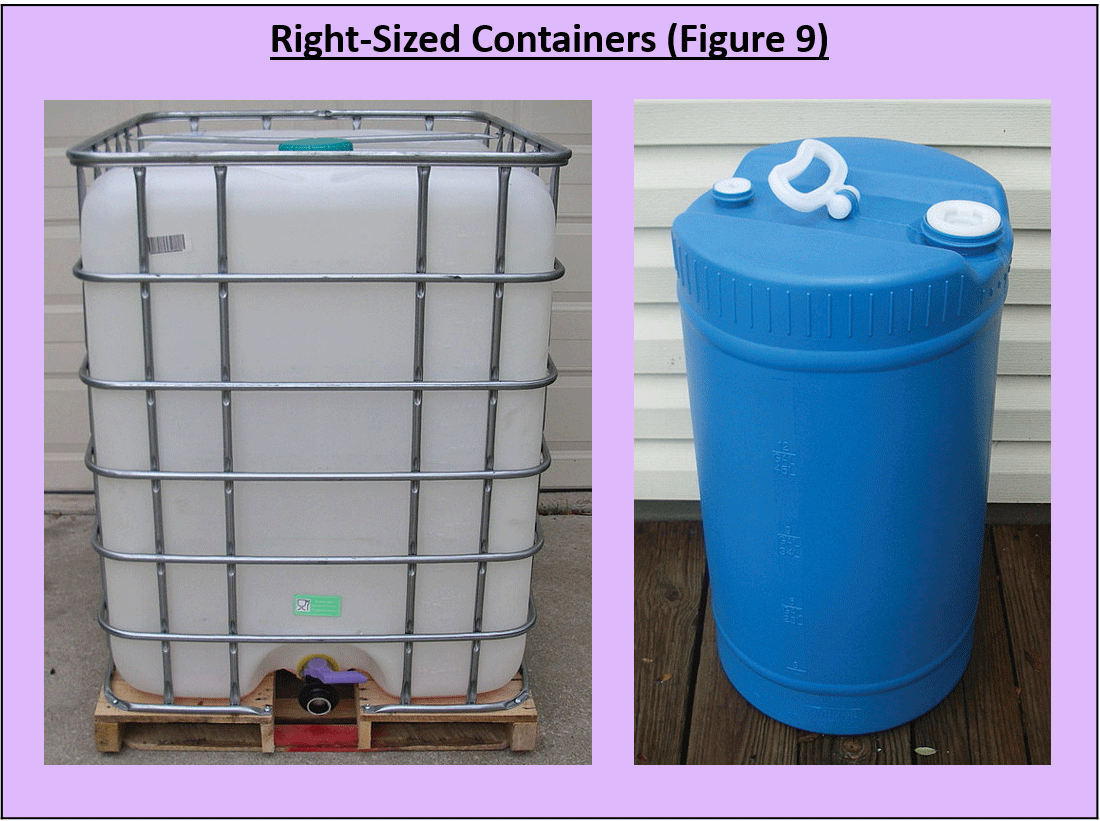


Point-of-Use Storage


POUS systems dramatically reduce the time and walking distance employees must devote to obtaining chemicals and materials needed for


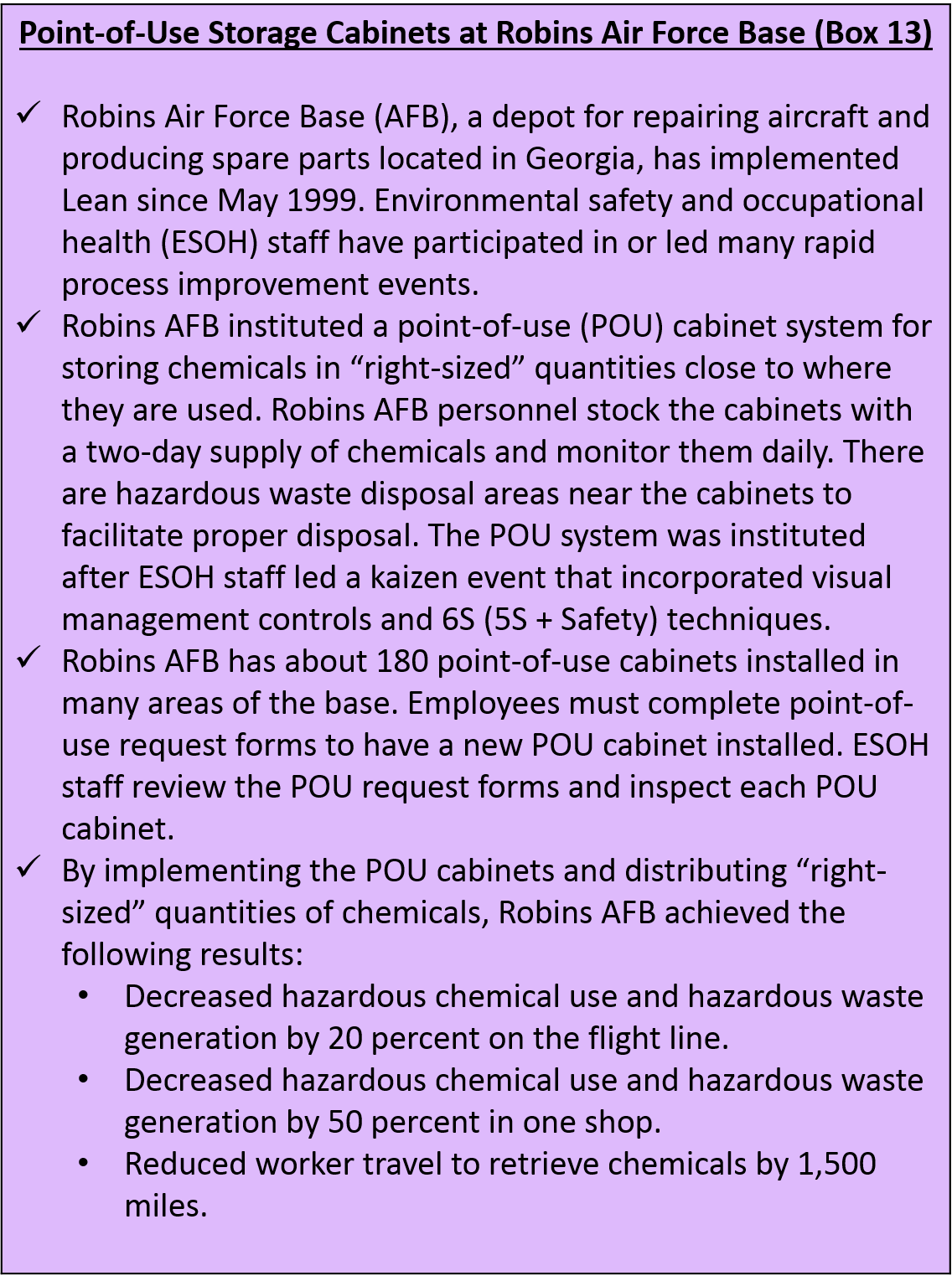
Lean Approaches to Chemical and Hazardous Waste Management
Lean thinking and methods can also transform how an organization approaches chemical and hazardous waste management. First, some companies have turned to their supply chain or external partners for strategic chemical and waste management services. By “servicizing” chemical procurement, some Lean companies have increased focus and incentives for eliminating the non-value-added aspects of chemical use. Second, some companies have used Lean methods, such as value stream mapping and kaizen events, to directly improve chemical and waste management work processes.
Chemical Management Services


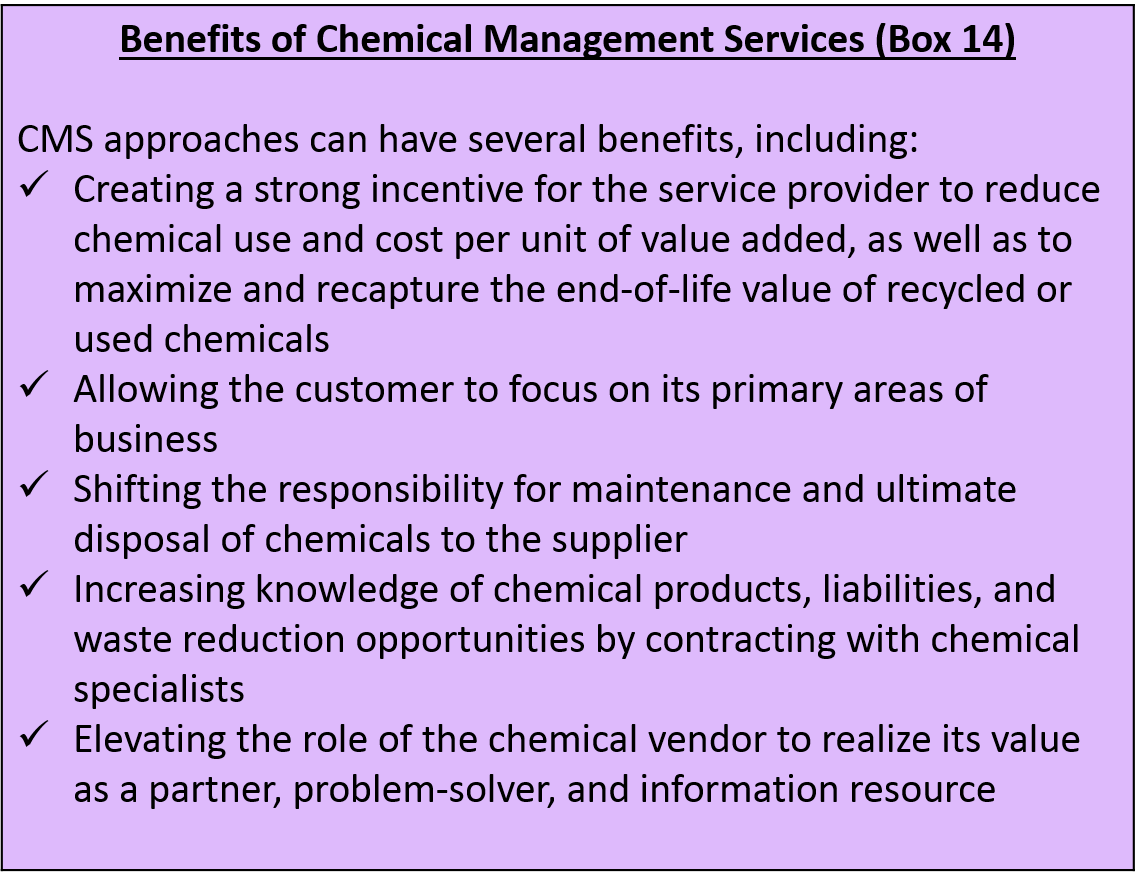
Applying Lean Methods to Chemical and Waste Management
Some companies have focused Lean value stream mapping and kaizen events specifically on chemical and hazardous waste management support processes. Lean events can be used to streamline and improve a variety of EHS support functions that relate to chemicals and hazardous waste, including:
- Chemical selection and procurement processes
- Chemical handling and inventory management
- Management of Material Safety Data Sheets
- Chemical handling and hazardous waste training activities and tracking
- Hazardous waste labeling, manifesting, and recordkeeping procedures
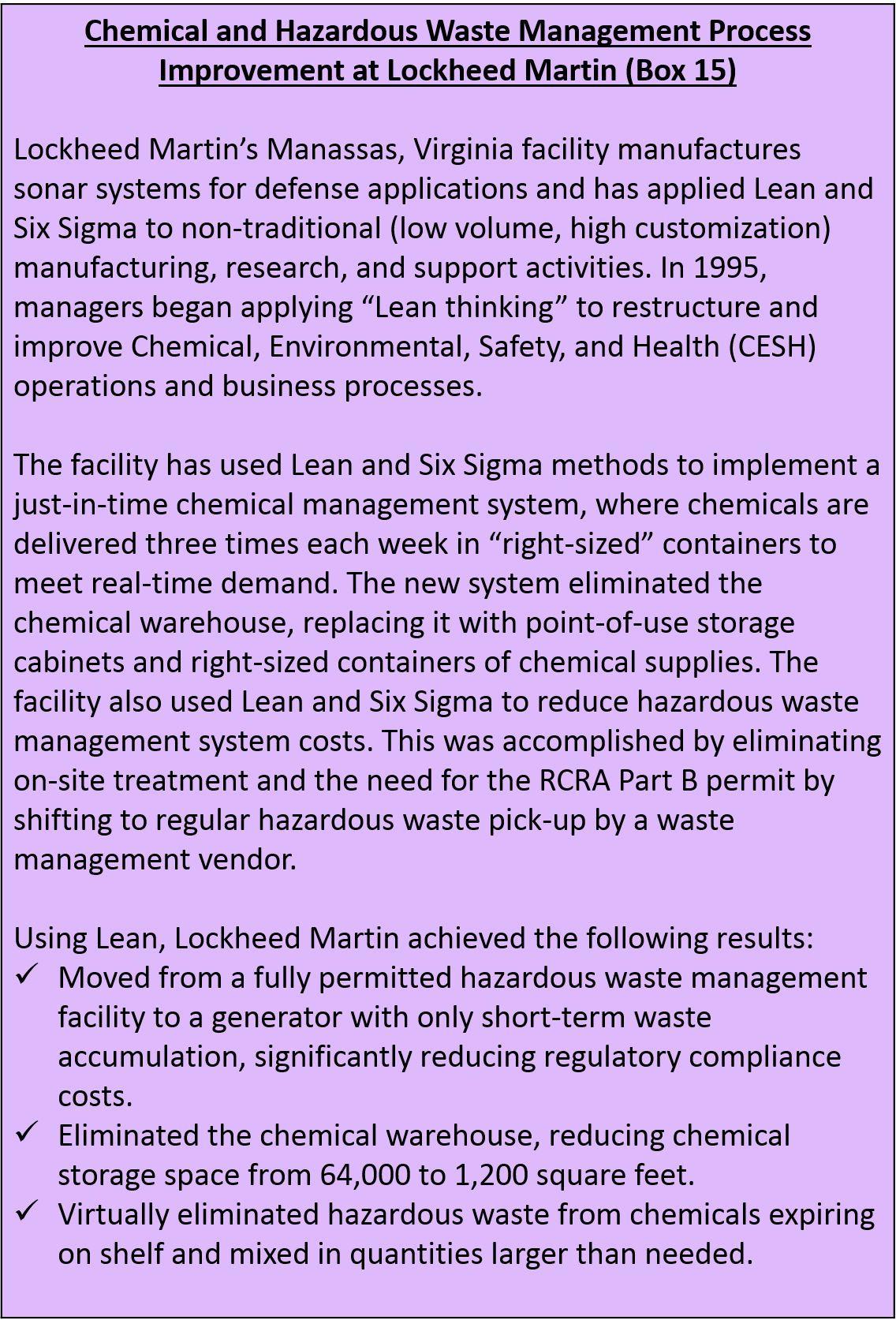
Footnotes
1 U.S. EPA, “Lean Manufacturing and the Environment,” October 2003, p. 25.
2Chemical Services Partnership, “What is CMS?”
Toolkit Navigation
- Contents & Acknowledgements
- Executive Summary
- Preface
- Chapter 1: Introduction
- Chapter 2: Chemicals Overview
- Chapter 3: Driving Out Chemical Waste with Lean Events
- Chapter 4: Chemical Management in the Lean Organization
- Chapter 5: Managing Chemicals in Lean Workspaces
- Chapter 6: Lean Product and Process Design Methods
- Chapter 7: Conclusion
- Appendix A: Chemical Resources
- Appendix B: Material Safety Data Sheet Template Example
- Appendix C: Point-of-Use Storage Request Form Example