Discharges and the EPA's Standards of Performance
The EPA’s Vessel Incidental Discharge National Standards of Performance, promulgated in October 2024 pursuant to the Vessel Incidental Discharge Act, includes three general discharge standards that are applicable to all regulated discharges, as well as specific standards for 20 different equipment and systems onboard vessels. While specific standards were identified for these 20 equipment and systems, the EPA may determine that it is appropriate to add specific standards for additional equipment or systems in the future.
On this page:
General Discharge Standards
- General Operation and Maintenance
- Biofouling Management
- Oil Management
Specific Discharge Standards
- Ballast Tanks
- Bilges
- Boilers
- Cathodic Protection
- Chain Lockers
- Decks
- Desalination and Purification Systems
- Elevator Pits
- Exhaust Gas Emission Control Systems
- Fire Protection Equipment
- Gas Turbines
- Graywater Systems
- Hulls and Associated Niche Areas
- Inert Gas Systems
- Motor Gasoline and Compensating Systems
- Non-oily Machinery
- Pools and Spas
- Refrigeration and Air Conditioning
- Seawater Piping
- Sonar Domes
Sewage discharges from vessels are regulated separately under the Clean Water Act. For information regarding the regulations in place to control vessel sewage discharges, please visit the EPA’s Vessel Sewage Discharges webpage.
The EPA’s VIDA regulations also included information requirements and procedures for states to follow if they choose to petition the EPA to:
- Review any standard of performance, regulation, or policy (“review of standards”);
- Require the use of an emergency best management practice to address aquatic nuisance species or water quality concerns (“emergency order”);
- Establish additional requirements with respect to discharges in the Great Lakes; or
- Prohibit one or more types of vessel discharges into specific state waters (“no-discharge zone”).
The EPA’s standards of performance are to be accompanied by corresponding implementing regulations from the U.S. Coast Guard. The Coast Guard is currently working to develop and finalize the implementing regulations.
This page includes information regarding each of the different regulated discharges and a brief summary of each of the four state petition processes. The contents of this page are informational in nature and do not replace or alter the promulgated requirements in the regulations at 40 C.F.R. Part 139.
Summary of Discharges
Ballast Tanks
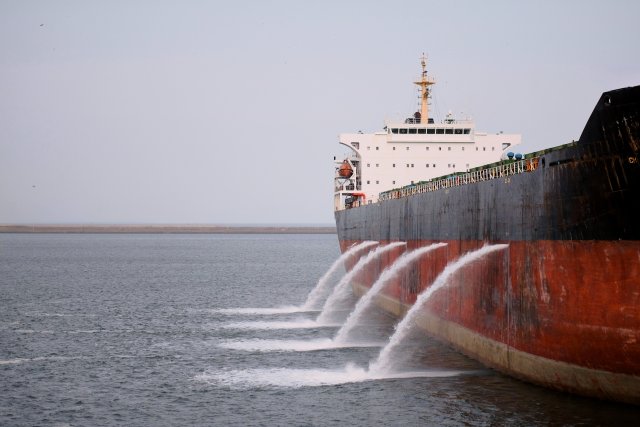
Ballast tanks are tanks onboard vessels designed to hold ballast water – any water, suspended matter and other materials taken onboard a vessel to control or maintain trim, draft, stability, or stresses of the vessel, regardless of how any such water or suspended matter is carried; or taken onboard a vessel during the cleaning, maintenance, or other operation of a ballast tank or ballast management system of the vessel.
Ballast capacities can range widely depending on the vessel type and type of deballasting equipment for the universe of vessels covered by the EPA’s rule. For example, passenger vessels typically have capacities of less than 5,000 cubic meters of water, whereas cargo/container ships may have capacities as high as 20,000 cubic meters.
Ballast water may contain toxic and nonconventional pollutants such as rust inhibitors, epoxy coating materials, zinc or aluminum (from anodes), iron, nickel, copper, bronze, silver and other material or sediment from inside the tanks, pipes, or other machinery. Importantly, ballast water may also contain organisms from where the water was taken up. Because ballast water may be taken up in one water body and discharged in another, these organisms may be moved from place to place via ballast water. In some cases, these organisms may establish new populations of aquatic nuisance species.
The introduction and spread of aquatic nuisance species is a significant environmental concern related to vessel operations, because these organisms can threaten the diversity and abundance of native species, as well as the commercial, agricultural, aquacultural and recreational uses of affected waters.
The requirements for ballast tanks are found in 40 C.F.R. 139.10.
Bilges
The vessel’s bilge is the lowest compartment of the vessel where drainage from interior machinery, engine rooms, pipes, decks and other sources accumulates. This drainage is collectively referred to as bilgewater and can include both conventional and toxic pollutants such as oil, grease, volatile and semi-volatile organic compounds, inorganic salts and metals.
Treatment of bilgewater onboard vessels is primarily targeted at reducing the parts per million of oil in the discharge due to its toxicity and harmful effects to aquatic organisms.
The requirements for bilges are found in 40 C.F.R. 139.11.
Boilers
Boiler blowdown is the discharge of water and constituents from the boiler during regular intervals to avoid concentration of impurities and at intermittent intervals for cleaning or other purposes. Boiler blowdown occurs on vessels with steam propulsion or a steam generator to control anti-corrosion and anti-scaling treatment concentrations and to remove sludge from boiler systems. Routine blowdown involves releasing a volume of about one to 10 percent of the water in the boiler system to manage the accumulation of solids and buildup of dissolved solids in the boiler water. Frequency of required blowdown varies, typically between once every two weeks to once every few months, although on some vessels blowdown may be as frequent as daily or even continuously. The constituents of boiler blowdown discharge vary according to the types of feed water treatment used, but may include toxic pollutants such as antimony, arsenic, cadmium, copper, chromium, lead, nickel, selenium, thallium, zinc and bis (2-ethylhexyl) phthalate.
The requirements for boilers are found in 40 C.F.R. 139.12.
Cathodic Protection
To prevent steel hulls and other metal structures from corroding, vessels use a method of corrosion control called cathodic protection. There are two types of cathodic protection - galvanic cathodic protection and impressed current cathodic protection. In both cases, anodes are connected to the metal being protected, creating a circuit that will result in the preferential corrosion of the anodes over the metal being protected (the cathode – e.g., the hull).
In the case of galvanic cathodic protection, “sacrificial anodes” or “galvanic anodes” are used that are a more reactive metal (typically magnesium, zinc, or aluminum) than the cathode. The protection relies on the corrosion of the anodes themselves. These anodes are easily replaced during vessel maintenance, as needed.
Impressed current cathodic protection, or ICCP, functions similarly, except that a direct current is passed through the metal being protected, such that its electrochemical potential is sufficiently high to prevent corrosion.
The discharge from either method of cathodic protection is continuous when the vessel is waterborne. Galvanic protection discharges include both toxic and nonconventional pollutants such as ionized zinc, magnesium and aluminum. The ICCP system, on the other hand, releases oxidants during the process, generally consisting of chlorinated and brominated substances from the reaction with seawater.
The requirements for cathodic protection are found in 40 C.F.R. 139.13.
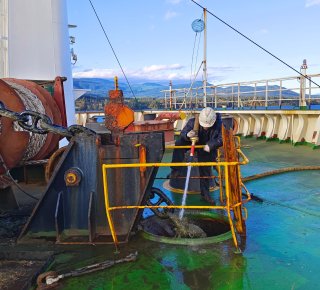
Chain Lockers
Chain lockers are storage areas onboard vessels that house anchors and chains. Water, sediment, biofouling organisms and contaminants – collectively referred to as “chain locker effluent” – can enter and accumulate in the chain locker during anchor retrieval and precipitation events.
Chain locker effluent can contain both conventional and nonconventional pollutants including organisms and residue from the inside of the locker itself, such as rust, paint chips, grease and zinc. The sump collects these liquids and materials that enter the chain locker prior to discharge or disposal.
The requirements for chain lockers are found in 40 C.F.R. 139.14.
Decks
Vessel decks can produce various discharges during a vessel’s normal operation, including deck runoff, deck washdown and deck flooding. Deck runoff consists of rain and other precipitation or condensation, as well as freshwater and seawater, that sprays or washes over the deck, well decks and bulkhead areas.
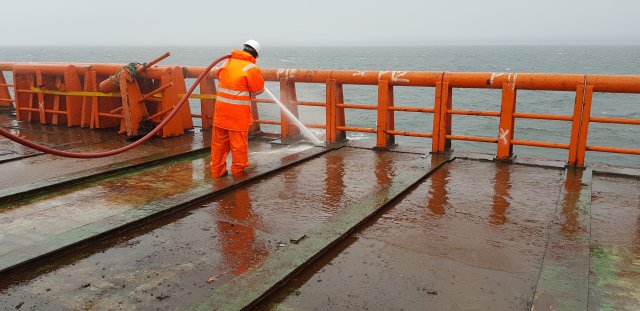
Deck washdowns consist of cleaners and freshwater or saltwater. Deck flooding generally consists of seawater from the flooding of a docking well (well deck) on a vessel used to transport, load and unload amphibious vessels, or freshwater from washing the well deck and equipment and vessels stored in the well deck.
The pollutants that may be present in discharges from the deck include both conventional and nonconventional pollutants such as oil, grease, fuel, cleaner or detergent residue, paint chips, paint droplets and general debris (e.g., trash).
The requirements for decks are found in 40 C.F.R. 139.15.
Desalination and Purification Systems
Distilling and reverse osmosis plants, also known as water purification plants or desalination systems, generate freshwater from seawater for a variety of shipboard applications. These include potable water for drinking, onboard services (e.g., laundry and food preparation) and high-purity feedwater for boilers. The wastewater from these systems is essentially concentrated seawater with the same constituents of seawater, including dissolved and suspended solids and metals; however, anti-scaling, anti-foaming and acidic treatments and cleaning compounds are also injected into the distillation system and can be present in the discharge. As such, the wastewater can contain toxic, conventional and nonconventional pollutants.
The requirements for desalination and purification systems are found in 40 C.F.R. 139.16.
Elevator Pits
Vessels with multiple decks are often equipped with elevators to facilitate the movement of equipment, people and cargo between decks. Liquids and debris from elevator operations accumulates in the bottom of the elevator shaft – the elevator pit – and may contain toxic, conventional and nonconventional pollutants such as oil, hydraulic fluid, lubricants, cleaning solvents, soot and paint chips. This elevator pit effluent can be emptied by gravity draining, discharged using the firemain, transferred to the bilge, or containerized for onshore disposal.
The requirements for elevator pits are found in 40 C.F.R. 139.17.
Exhaust Gas Emission Control Systems
Exhaust gas emission control systems reduce the sulfur oxides and nitrogen oxides in the exhaust from marine engines. The operation of these systems, however, produces washwater and residues. Two such systems are exhaust gas cleaning systems (EGCSs) and exhaust gas recirculation (EGR) systems.
EGCSs – commonly referred to as “scrubbers” – are named as such because they “scrub” sulfur oxides from the exhaust gases produced by marine diesel engines. Scrubbers may be used to comply with global emissions regulations in lieu of using low-sulfur fuel. EGCS operations produce an acidic washwater that contains toxic, conventional and nonconventional pollutants including sulfur compounds, polycyclic aromatic hydrocarbons (PAHs), and traces of oil, NOX, heavy metals and captured particulate matter.
There are three main types of scrubbers – open, closed and hybrid. Both open-loop and closed-loop systems are considered “wet” EGCS technologies, meaning that these systems use either seawater or freshwater to scrub the exhaust. Open-loop systems remove the contaminants from marine exhaust by running the exhaust through seawater sourced from outside the vessel and then discharging the resulting washwater back out to sea. In contrast, closed-loop systems use freshwater and inject caustic soda to neutralize the exhaust. A small portion of the washwater is bled off and treated to remove suspended solids that are held for onshore disposal. While this design is not completely closed-loop, it can operate in zero discharge mode for a period. Hybrid scrubbers are systems that can operate either in open- or closed-loop mode. At sea, these hybrid systems typically operate in open-loop mode, whereas in nearshore waters, harbors and estuaries, they operate in closed-loop mode.
EGR systems, on the other hand, are used to reduce nitrogen oxide emissions in marine exhaust. These systems minimize nitrogen oxide production by cooling part of the engine exhaust gas and then redirecting it back to the engine air intake. The addition of the recirculated engine exhaust reduces the amount of oxygen available for fuel combustion, reducing peak combustion temperatures and resulting in significantly reduced nitrogen oxide formation. The cooling of the recirculated exhaust gas causes condensation of water vapor formed during combustion, generating a continuous wastewater stream (bleed-off water) from the condensate. This condensate can contain toxic, conventional and nonconventional pollutants such as particulates (soot, metals and hydrocarbons) and sulfur. In some cases, the EGR systems also capture oils, for example from cylinder lubrication, that are emitted from the combustion process and collected as part of the scavenged air. Excess bleed-off water that accumulates in an EGR system is typically discharged overboard following treatment, and any residues are held for onshore disposal. On vessels that use high-sulfur fuel and an EGCS, the EGR system bleed-off water is often combined with the EGCS washwater and processed as a combined waste stream.
The requirements for exhaust gas emission control systems are found in 40 C.F.R. 139.18.
Fire Protection Equipment
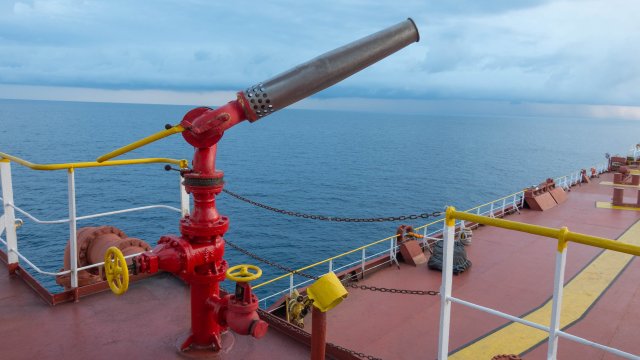
Fire protection equipment includes all components used for fire protection including, but not limited to, firemain systems, sprinkler systems, extinguishers and firefighting agents, such as foam. Firemain systems draw in water through the sea chest to supply water for fire hose stations, sprinkler systems and firefighting foam distribution stations. Firemain systems are also frequently used for other purposes onboard the vessel, such as for deck and equipment washdowns and anchor/anchor chain rinsing.
The water in the firemain systems can contain metals that are produced from the corrosion and erosion of pipes, valves and pumps. Additionally, firefighting foams can be added to the system and mixed with seawater to control emergencies onboard the vessel. The constituents of firefighting foam can vary by manufacturer but can include persistent, bioaccumulative, toxic and non-biodegradable ingredients. Discharges of firefighting foam can also contain phthalate, copper, nickel and iron, which can be constituents in the composition of firemain piping. Fluorinated firefighting foam contains per- and poly-fluoroalkyl substances, commonly known as PFAS, or their precursors; examples include aqueous film forming foam, alcohol resistant aqueous film forming foam, film-forming fluoroprotein foam, fluoroprotein foam, alcohol-resistant fluoroprotein foam and other fluorinated compounds. Many PFAS are toxic and/or carcinogenic. Non-fluorinated firefighting foam does not contain PFAS or their precursors; examples include protein foam, alcohol-resistant protein foam, synthetic fluorine free foam and synthetic alcohol-resistant fluorine free foam.
The requirements for fire protection equipment are found in 40 C.F.R. 139.19.
Gas Turbines
Gas turbines are used on some vessels for propulsion and electricity generation. Occasionally, they must be cleaned to remove byproducts that can accumulate and affect their operation. The byproducts and cleaning products can include toxic and conventional pollutants including salts, lubricants, combustion residuals, naphthalene and other hydrocarbons. Additionally, due to the nature of the materials being cleaned, there is a higher probability of heavy metal concentrations.
The requirements for gas turbines are found in 40 C.F.R. 139.20.
Graywater Systems
Graywater is water drained or collected from sources such as galleys (kitchens), showers, baths, sinks, laundry facilities and water fountains. Graywater discharges can contain bacteria, pathogens, oil and grease, detergent and soap residue, metals (e.g., cadmium, chromium, lead, copper, zinc, silver, nickel, mercury), solids and nutrients. The volume of graywater generated onboard a vessel depends on the number of people and types of activities that occur onboard a specific vessel. For example, vessels with overnight accommodations and onboard leisure activities – such as cruise ships – are expected to generate higher volumes of graywater than a working vessel because passengers and crew are using more water for bathing, food preparation and other such activities.
While graywater is frequently combined with sewage (blackwater) in the piping systems onboard vessels, sewage is not covered by this rule. More broadly, drainage from toilets, urinals, hospitals or other medical spaces or equipment, animal spaces and cargo spaces are not considered graywater for purposes of the EPA’s rule. Information on vessel sewage discharge requirements are available on the EPA’s Vessel Sewage Discharges webpages.
The requirements for graywater systems are found in 40 C.F.R. 139.21.
Hulls and Associated Niche Areas

For purposes of the EPA’s rule, the requirements for discharges from hulls and associated niche areas is broken down into two broad categories – coatings and cleaning. Vessel equipment and systems that are immersed in or exposed to the aquatic environment can accumulate organisms such as plants, animals and microorganisms – collectively referred to as “biofouling.” Biofouling can damage the vessel’s hull and other equipment, as well as increase drag as biofouling builds up on the vessel’s surfaces. This results in decreased speeds and reduced fuel efficiency. Additionally, biofouling is one of the main vectors for the transportation and introduction of aquatic nuisance species. The EPA’s regulations try to limit the discharge of biofouling by preventing it from accumulating in the first place through the application of coatings and cleaning it when it does appear.
- Coatings: Vessel hulls are often coated with anti-fouling compounds to prevent or inhibit the attachment and growth of biofouling organisms. Selection, application and maintenance of an appropriate anti-fouling coating type and thickness according to vessel profile is critical to effective biofouling management, and therefore preventing the introduction and spread of aquatic nuisance species from the vessel hull and associated niche areas. Multiple types of anti-fouling coatings are available for use, including hard, controlled depletion or ablative, self-polishing copolymer and fouling release coatings. Anti-fouling coatings may employ physical, biological, chemical, or a combination of controls to reduce biofouling. Those that contain biocides prevent the attachment of biofouling organisms to the vessel surface by continuously leaching substances that are toxic to aquatic life. The most commonly used anti-fouling biocide is copper. Manufacturers may also combine copper with other biocides, often called booster biocides, to increase the effectiveness of the anti-fouling coating. Cleaning the anti-fouling coating typically results in pulses of biocide into the environment, particularly if surfaces are cleaned within the first 90 days following application.
- Cleaning: Cleaning of hulls and niche areas, including the removal of any biofouling, is an important component of hull and niche area maintenance. While niche areas account for a small percent of the total wetted surface area of a vessel, the majority of biofouling accumulates there. Vessels generally use two types of cleaning techniques to remove biofouling: cleaning while in drydock and in-water cleaning. Techniques for in-water cleaning of vessel surfaces can be broadly separated into two categories: (1) in-water cleaning with capture, or IWCC; and (2) in-water cleaning without capture. IWCC is the use and operation of a cleaning system for vessel surfaces that is designed to capture and transport coatings and biofouling organisms to an adjacent barge or shore-based facility for collection and processing. The waste stream is processed by a separate service provider, not the vessel. As such, the EPA views discharges from IWCC as similar to the discharge of treated ballast water from a barge-based or shore-based treatment facility, which are not subject to regulation under the Vessel Incidental Discharge Act (and by extension, the EPA rule). In-water cleaning without capture refers to any in-water cleaning techniques that do not use a capture device, and discharges from in-water cleaning without capture are regulated under the EPA’s rule.
The requirements for hulls and associated niche areas are found in 40 C.F.R. 139.22.
Inert Gas Systems
Inert gas is used on tankers for several reasons, with one of the primary uses being to control the oxygen levels in the atmosphere of cargo and ballast tanks to prevent explosion and suppress flammability. Inert gas system discharges consist of scrubber washwater and water from deck water seals when used as an integral part of the inert gas system.
Per 40 C.F.R. 139.23, there are no additional discharge-specific requirements that apply to the discharge of washwater from an inert gas system and deck seal water when used as an integral part of that system. However, discharges from inert gas systems must meet the general discharge requirements related to General Operation and Maintenance, Biofouling Management, and Oil Management.
Motor Gasoline and Compensating Systems
Motor gasoline compensating system discharge is the discharge of seawater that is taken into motor gasoline tanks to replace the weight of fuel as it is used and eliminates free space where vapors could accumulate. The compensating system is used for fuel tanks to supply pressure for the gasoline and to keep the tank full to prevent potentially explosive gasoline vapors from forming. The seawater is discharged when the vessel refills the tanks with gasoline or when performing maintenance. The discharge can contain both toxic and conventional pollutants including residual oils or traces of gasoline constituents, which can include alkanes, alkenes, aromatics (e.g., benzene, toluene, ethylbenzene, phenol and naphthalene), metals and additives. Most vessels by design do not produce this discharge.
The requirements for motor gasoline and compensating systems are found in 40 C.F.R. 139.24.
Non-Oily Machinery
Non-oily machinery wastewater is the combined wastewater from the operation of distilling plants, water chillers, valve packings, water piping, low- and high-pressure air compressors, propulsion engine jacket coolers, fire pumps and seawater and potable water pumps. Non-oily machinery wastewater systems are intended to keep wastewater from machinery that does not contain oil separate from wastewater that has oil content. While non-oily machinery wastewater discharges may not have oil, they can include a suite of conventional and nonconventional pollutants including metals and organics.
The requirements for non-oily machinery are found in 40 C.F.R. 139.25.
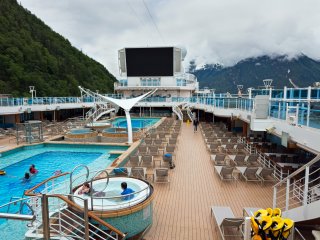
Pools and Spas
Some vessels may have freshwater or seawater pools or spas onboard that contain water treated with chlorine or bromine for disinfection. These disinfectants are nonconventional pollutants that may be discharged by the vessel when pools or spas are drained.
The requirements for pools and spas are found in 40 C.F.R. 139.26.
Refrigeration and Air Conditioning
Condensation from cold refrigeration or evaporator coils of air conditioning systems drips from the coils and collects in drip troughs that typically channel to a drainage system. The condensate discharge may contain toxic, conventional and nonconventional pollutants including but not limited to detergents, seawater, food residue and trace metals.
The requirements for refrigeration and air conditioning systems are found in 40 C.F.R. 139.27.
Seawater Piping
Seawater piping systems carry seawater to various locations onboard the vessel via a network of pipes and pumps. This seawater is critical to the proper functioning of a vessel and is used for activities such ballasting and firefighting, as well as in a variety of systems (e.g., engines, hydraulics, cleaning equipment, refrigeration, toilet systems). Some components of seawater piping systems, including sea chests, sea inlet pipes and overboard discharges, are also considered niche areas, and therefore are subject to the requirements for hulls and associated niche areas (40 C.F.R. 139.22).
As discussed in the section on hulls and associated niche areas, these systems are prone to biofouling and can result in the discharge of biofouling organisms. Ensuring that seawater piping systems are unobstructed by biofouling is also vital to vessel operations. Blockages of internal seawater piping, such as those for engine cooling and firemain systems, can threaten the integrity of the vessel structure and impede safe operation of the vessel.
Seawater piping systems can be fitted with Marine Growth Prevent Systems to prevent biofouling by organisms drawn in along with the intake water. The most common MGPSs for seawater include sacrificial anodic copper systems and chlorine-based dosing systems. The sacrificial anodic copper systems work in a similar fashion to what was described in the “Cathodic Protection” section on this page. Typically, copper anodes and aluminum or ferrous anodes are mounted in the piping system and connected to a control panel. The copper anodes release ions that prevent the settlement of organisms on the piping system surfaces. Chlorine-based dosing systems, on the other hand, inject a small amount of chlorine near the seawater intakes to prevent biofouling.
Seawater piping system discharges include non-contact engine cooling water, hydraulic system cooling water, refrigeration cooling water and freshwater lay-up wastewater. Such systems use ambient seawater to absorb the heat from heat exchangers, propulsion systems and mechanical auxiliary systems. The water is typically circulated through an enclosed system that does not come in direct contact with machinery, but still may contain sediment from water intake, traces of hydraulic or lubricating oils and trace metals leached or eroded from the pipes within the system. Additionally, because it is used for cooling, the effluent will have an increased temperature.
The requirements for seawater piping systems are found in 40 C.F.R. 139.28.
Sonar Domes
Sonar domes house detection, navigation and ranging equipment and are filled with water to maintain their shape and pressure. They are typically found on research vessels but may be present on other vessel classes. Sonar dome discharges occur when the water in the dome is drained for maintenance or repair. The discharge of seawater or freshwater from the dome may contain leachate from anti-fouling materials as well as toxic pollutants including zinc, copper, nickel and epoxy paints. Sonar domes may also leach materials such as anti-fouling agents, plastic, iron and rubber from the exterior surface of the dome.
The requirements for sonar domes are found in 40 C.F.R. 139.29.
State Petitions
The EPA’s rule includes information requirements and procedures for states to follow if they choose to petition the EPA to:
- Review any standard of performance, regulation, or policy;
- Require the use of an emergency best management practice to address aquatic nuisance species or water quality concerns (“emergency order”);
- Request additional requirements with respect to discharges in the Great Lakes; or
- Apply to the EPA to completely prohibit one or more types of vessel discharges into specific state waters (“no-discharge zone”).
Petition to Review Any Standard of Performance, Regulation, or Policy
A governor of a state may submit a petition to the EPA to review any standard of performance, regulation, or policy if there exists new information that could reasonably result in a change to the standard of performance, regulation or policy; or a determination on which the standard of performance, regulation, or policy was based.
The petition must be signed by the Governor (or a designee) and include the purpose of the petition; any applicable scientific or technical information that forms the basis of the petition; the direct and indirect benefits, as well as the costs to the affected classes, types and/or sizes of vessels, if the requested petition were to be granted.
Petition for an Emergency Order
A governor of a state may submit a petition to the EPA to issue an emergency order in circumstances where there is a risk of introduction or establishment of an aquatic nuisance species or where the adverse effects of a discharge contribute to a violation of a water quality requirement.
The petition must be signed by the Governor (or a designee) and include:
- The purpose of the petition;
- Any applicable scientific or technical information that forms the basis of the petition; and
- The direct and indirect benefits if the requested petition were to be granted.
Petition for Enhanced Great Lakes System Requirements
The Vessel Incidental Discharge Act identifies a process for establishing enhanced standards or requirements to apply within the Great Lakes System in lieu of any comparable standards or requirements in the EPA’s rule. The Act lays out many of the procedural requirements, but ultimately, the petition submitted to the EPA and the U.S. Coast Guard by Great Lakes Governors must include an explanation regarding why the applicable standard of performance or other requirement is:
- At least as stringent as a comparable standard of performance or other requirement in the final rule; and
- In accordance with maritime safety and applicable maritime and navigation laws and regulations.
If the proposed standard of performance would impose any additional equipment requirement on a vessels, then the proposal must be endorsed by all Great Lakes Governors. Otherwise, the proposal must be endorsed by at least five Great Lakes Governors.
Application for a No-Discharge Zone
A governor of a state may apply to the EPA to establish a regulation prohibiting one or more discharges, whether treated or not treated, into some or all of that state’s waters. The application must be signed by the Governor (or a designee) and include:
- A narrative explanation of the location of the proposed waters and a map delineating the boundaries of the requested prohibition using geographic coordinates;
- A certification that a prohibition of the discharge(s) would protect and enhance the quality of the specific waters within the state to a greater extent than the applicable federal standard provides;
- A detailed analysis of the direct and indirect benefits of the requested prohibition for each individual discharge for which the state is seeking a prohibition;
- A table identifying the types and number of vessels operating in the waterbody and a table identifying the types and number of vessels that would be subject to the prohibition;
- A table identifying the location, operating schedule, draft requirements, pumpout capacity, pumpout flow rate, connections and fee structure of each existing facility capable of servicing the vessels that would be subject to the prohibition and available to receive the prohibited discharge;
- A description of the wastewater handling procedures of each facility, including information on how wastewater is stored, transported, treated and/or disposed by each facility;
- A map indicating the location of each stationary facility, and the coverage area of each mobile facility;
- A detailed analysis of the impacts to vessels subject to the prohibition, including a discussion of how these vessels may feasibly collect and store the discharge, the extent to which retrofitting may be required, costs that are incurred as a result of the discharge prohibition, and any safety implications.
The EPA must then determine whether the prohibition of the discharge(s) would protect and enhance the quality of the specified waters within the state, and whether adequate facilities for the safe and sanitary removal and treatment of the prohibited discharge(s) are reasonably available.